Tulip Removes Work Injury Hazard Using Danish Pallet Invention
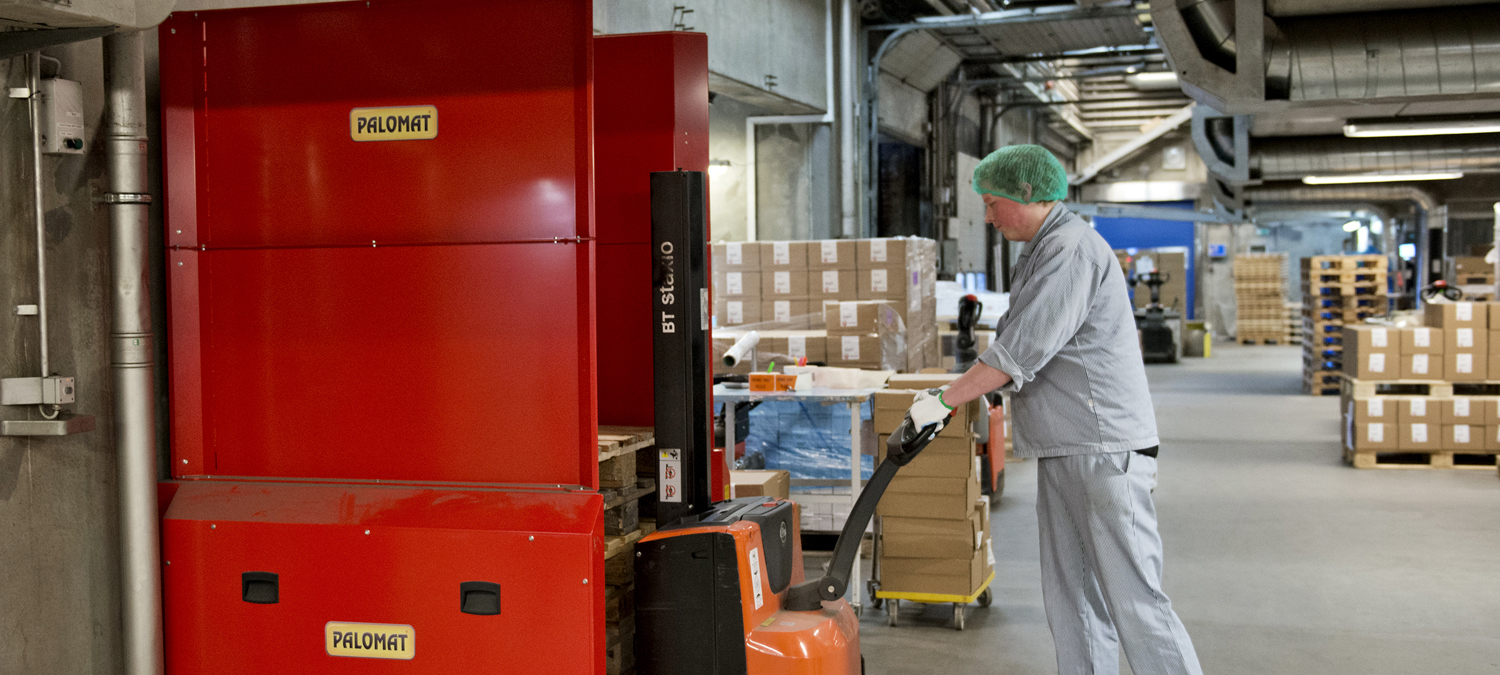
Improved workflow that protects employees from injuries
The manual lifting of pallets has been eliminated at the Shipping Department of the Tulip retail packing centre in Denmark. Pallet handling is now automated with a PALOMAT® Greenline. This has created better workflow, which has also ended related work injuries.
Improved work environment
Happier employees
Reduced work-related injuries
Improved workflow
Challenge
The company Tulip handles up to six tons of pallets per day. Pallet handling was manual, and everything was lifted by physical strength. Many employees experienced back problems, were tired and worn out after their workday. There were frequent sick leaves due to injuries.
Solution
The company installed a PALOMAT® Greenline in their production. The factory manager came across PALOMAT® on social media and immediately became curious about whether the pallet magazine could help solve their challenges. Shortly after the installation of the first machine, they invested in machine number two.
Profit
The PALOMAT® Greenline relieves Tulip's employees and has provided them with a better working environment. The heavy manual pallet lifts are eliminated, and the employees are happier and not tired when they return home from work. The PALOMAT® pallet magazine helps reduce work-related injuries and reports of sickness.
The employees at Tulip’s Shipping Department were sceptical at first when Factory Manager Dennis Harder Sørensen introduced a new Greenline pallet magazine from PALOMAT®. However, after a short period of time, the employees were very happy with the automated palletising system.
The department handles up to six tons of pallets a day, which previously had to be lifted manually – and according to Dennis Harder Sørensen, it was taking a physical toll on employees.
"Previously the pallets had to be tipped manually from a stack of 12–13 pallets, which was physically strenuous for our employees. Fortunately, that’s now a thing of the past, because now have a fully automated palletising system that has removed the heavy lifting."
"The new palletising system has of course changed the employees’ workflow but we have retained the same volume as before. The Greenline pallet magazine is actually a cheap solution, and it is a valuable investment for our employees, who now have a better working environment, where they are exposed to fewer work injuries."
Dennis Harder Sørensen, Factory Manager at Tulip
No More Work Injuries
Greenline is a fully automated pallet magazine that handles all pallets at floor level. All employees need to do is insert or remove the empty pallets using a forklift truck or hand pallet truck, and the palletising system does the stacking and destacking.
The employees in Tulip’s Shipping Department had previously experienced back injuries. This included production employee Jonas Christensen, who was forced to stay at home at the beginning of 2018 because of an injured back. He is already back working in the department, where he is benefiting from the new pallet magazine:
"Before I would get tired after a long working day but this here – it just works. I don’t have a sore back anymore and I don’t even feel any discomfort after my accident. I’m really satisfied with the new pallet magazine here on the site. It ‘s not very often you see a new machine being well received, but this one was.", says Jonas Christensen.
According to Dennis Harder Sørensen, the automated palletising system from PALOMAT® has eliminated the risk of back injuries at Tulip’s Shipping Department and has resulted in employees who are more satisfied.
"The pallet magazine minimises inconvenience and prevents potential injuries among our employees, who also tell us that they are less tired when they return home from work. So overall, the automation of pallet handling has created a better work environment at our factory and given us happier employees."
Dennis Harder Sørensen, Factory Manager at Tulip
The Whole Thing Started on Facebook
According to Dennis Harder Sørensen, him and his colleagues had discussed several times about the possibility of acquiring a palletising system, but they could not find the right solution.
But one day Dennis Harder Sørensen found it on Facebook, when the factory manager saw a competition that had been started by PALOMAT®. However, it was not the prize (a cake) that caught Dennis Harder Sørensen’s attention. It was the palletising system, which stood in the background of the Facebook competition’s image:
"When I saw the PALOMAT® competition on Facebook, I quickly called them to learn more about the pallet magazine that was on the image. We didn’t know of PALOMAT® or their products, so we obtained a Greenline pallet magazine for a trial run, and it proved to be the perfect solution."
"In fact our employees were so satisfied with the new system that after only a month, they asked for another pallet magazine. They had personally found a space in the department where the palletising system could stand.", says Dennis Harder Sørensen and adds that the management are now considering whether other departments at the factory need an automated palletising system.
Contact us
We are ready to answer your
questions and have a conversation
about the possibilities for optimizing
your pallet flow.
Send us a message or call us at
+45 9669 4710