LINAK A/S saves employees from lifting heavy pallets and increases productivity
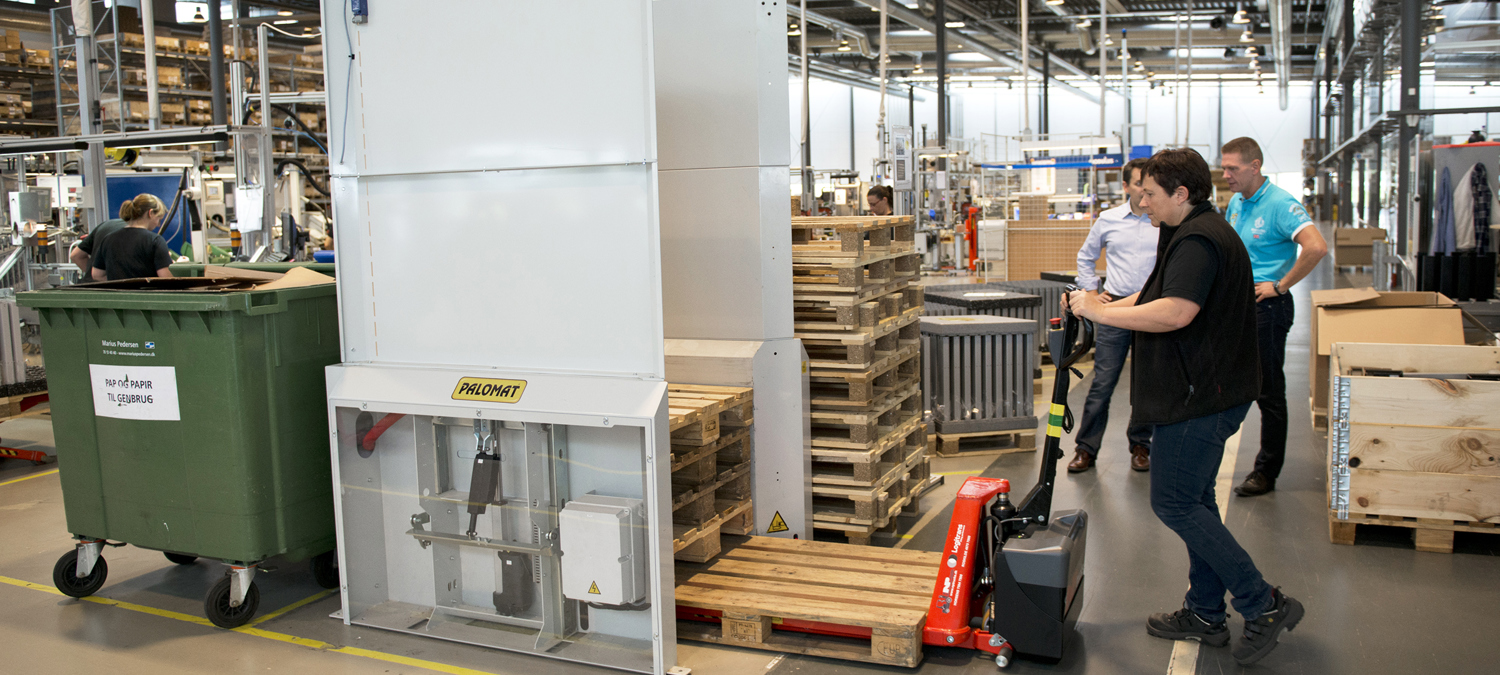
PALOMAT® GreenlineIn need for alternative pallet handling
Changing demands in the market resulted in a switch from single-use pallets to Euro pallets. Because of this, it became necessary to review the process of handling empty pallets and the choice was on three PALOMAT Greenline pallet magazines.
Improved working environment without manual pallet handling
Order and structure in production
Neat and even pallet stacks
Increased productivity
Challenge
The company Linak A/S handled approximately 1000 pallets every week. The transition to EUR pallets made manual pallet handling more challenging, and often multiple employees were required to handle the pallets. Pallet handling was time-consuming and posed risks of workplace injuries.
Solution
The company invested in 3 PALOMAT® Greenline units as they are cost-effective and flexible for production. PALOMAT® Greenline is 100% electric and Plug'n'Play, making it easy to move around in production as needed.
Benefit
PALOMAT® Greenline pallet magazines have eliminated the strenuous manual pallet handling and reduced the risk of workplace injuries. The working environment has improved, and there is more order. It only requires one person to get the tasks done, freeing up resources for other tasks, thereby increasing productivity.
At LINAK A/S, the Deskline division handles around 1,000 pallets per week. Loaded pallets are transported by forklift truck from the warehouse to the production cells. Once empty, height-adjustable pallet lifters transport the pallets to the PALOMATs where the PALOMATs perform auto stacking of the pallets. Prior to this investment, employees manually helped each other to stack the pallets.
"As a result of increasing requests from the market due to pallet stability, we replaced our light single-use pallets with EUR-pallets. But the EUR-pallets are a lot heavier. To make sure that we don’t get work injuries when lifting the heavy pallets, we were forced to look at other solutions for pallet handling,”
Torben Levisen, Operations Manager at LINAK A/S
“We quickly zeroed in on pallet magazines, but we wanted to look into whether to choose a pneumatic or electric-powered solution.” says Torben Levisen and continues;
“In the end we went for the electric-powered option since it is more economical to operate compared to the pneumatic machines. Moreover, if changes would be made in our production, it is more flexible since it can be quickly relocated and simply connected to the mains.”
“Now we can use the hand pallet truck all the way, and the previous risk of work injuries from heavy lifting has been eliminated. Besides now only a single person can attend to pallet handling even when the stack is high. Visually, we also achieve a more structured production environment.”, ends Torben Levisen.
Facts: LINAK A/S is the world’s leading player in the development and production of linear electrical actuators. LINAK A/S was established in 1907 and today has 1,600 employees across 35 countries worldwide.
Contact us
We are ready to answer your
questions and have a conversation
about the possibilities for optimizing
your pallet flow.
Send us a message or call us at
+45 9669 4710